~電池式「ぴこぴこ」を実現した夢の技術、
超省電力メタンセンサーの開発~
世界初 電池式家庭用ガス警報器
「ぴこぴこ」の開発
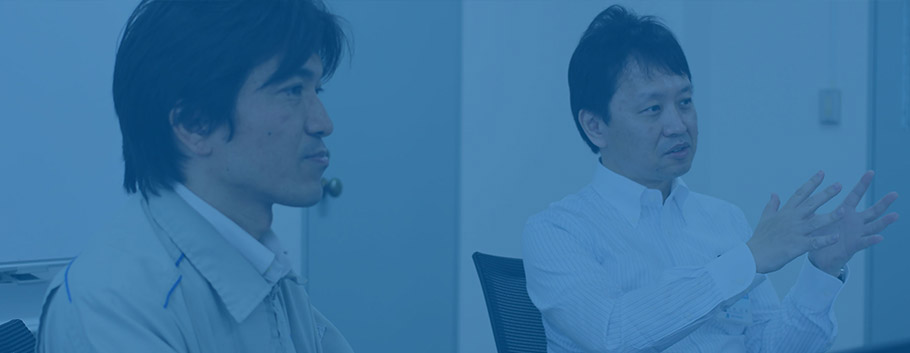
DEVELOPER INTERVIEW
開発者インタビュー
電池式「ぴこぴこ」を実現した夢の技術、
超省電力メタンセンサーの開発
世界初 電池式家庭用ガス警報器
「ぴこぴこ」の開発
「ぴこぴこ」は、万一のガス漏れや不完全燃焼による室内での空気の汚れを検知し警報する家庭用ガス警報器。発売以来、改良を重ね、たくさんのご家庭に安心・安全をお届けしてきました。
これまで蓄積してきた技術の粋を集め、16年もの月日をかけて挑んできた電池式「ぴこぴこ」用ガスセンサーの開発プロジェクト。次々と立ちはだかる難問をどのように解決したのか、夢の技術をなぜ実現できたのかなど、製品誕生までの開発秘話を2名の開発者が語ります。
MEMBER
エネルギー技術研究所
-
[副理事]エグゼクティ
ブリサーチャー(理学博士)
大西 久男 -
表面科学チーム[副課長]
野中 篤
社会のニーズから生まれた、高性能な家庭用
ガス警報器
「ぴこぴこ」が誕生した頃は、まだ、おしゃべりする警報器って珍しかったのでは。
- 大西
-
「ぴこぴこ」の発売は1980年。初代「ぴこぴこ」はガス漏れを検知すると「ピッピッ」と鳴るだけでしたが、その後、様々な家電製品の発する電子音と区別しやすくするため、「ガスが漏れていませんか?」という音声で警報をお知らせするようになりました。当時はまだ、しゃべる機器や家電製品は珍しかったのですが、音とメッセージでお客さまに注意を促すという先進的な機能を当社ではいち早く取り入れました。
電池式「ぴこぴこ」は電源コードがなくなり、すっきりしたデザインに。現行機の課題はどのようなことでしたか。
- 大西
-
現行機の「ぴこぴこ」はガスを検知するセンサーの消費電力が大きく、AC100V電源が必要です。また、都市ガスは空気より軽いため、天井の近くに取り付けないといけません。「ぴこぴこ」の販売を始めた頃は、台所の天井近くに換気扇用コンセントのあるお宅が多かったのですが、換気扇のビルトイン化が進み、コンセントは床の近くにしかないお宅が増えたため、特に壁掛けタイプにおいてはコードを床上付近から天井近くまで配線しないといけないお宅が増えたということが一番の課題でした。そのようなことから、「電源コードが邪魔なので、無くせないのか」とのお声が強くなってきました。
見栄えの悪さから「ぴこぴこ」の取り付けを見送られるお客さまが多かったということですね。
- 大西
-
特に、新築やリフォームされたお宅だと「せっかくのきれいな新居のキッチンに見栄えの悪いコードを壁にはわせるのは避けたい」と「ぴこぴこ」の取り付けを躊躇されるご家庭も多いと聞いています。やはり、そのような理由でお客さまの安心・安全を守る「ぴこぴこ」を取り付けることができないというのは、ガスサービスをお届けする私たちとしてとても残念なことですから。私たちは取り付けをしやすくするための技術研究に取り組むなど、常に時代のニーズに合った製品をお届けしています。電池式「ぴこぴこ」も「ユーザースタンスで物事を考える」という当社の基本姿勢から誕生した画期的な新製品なんです。
35年もの歴史がある「ぴこぴこ」ですが開発の背景としてどのようなことがあったのでしょうか。
- 大西
-
昭和50年代、一般住宅の窓材にもアルミサッシが使われるようになったことで住宅の高気密化が急速に進み、わずかなガス漏れによっても室内にガスが滞留する懸念が社会的にクローズアップされました。このような経緯から、集合住宅業界の一部では「目に見えないガス漏れが自動的にわかるような装置がないと心配」、「ガスは危ないから使わないほうがいいのでは」というような話まであったようです。
これを受けて大阪ガスでは家庭用ガス警報器の研究開発に着手されたのですね。
- 大西
-
他社さんがマイコンメーターによる間接的ガス漏れ検知技術に取り組んだのに対し、大阪ガスでは実際にガスが使われている場所でガス漏れを直接検知する警報器の実用化に注力し、研究開発をスタートさせました。このことが今回ご紹介するガスセンサー技術開発のきっかけとなりました。私たちは、当時実用化されつつあったLPGガス用警報器を参考に、都市ガスの主成分であるメタンを検知するセンサーの技術開発を始め、1980年に初代「ぴこぴこ」を発売しました。その後も、ガスセンサーのガス検知や性能変化のメカニズムを突き止めたほか、長寿命化を目指して性能保証期間を3年から5年に改良するなど業界を先導する研究開発を推進してきました。
(右)世界初の電池式家庭用ガス警報器 (左)従来機
省電力化への挑戦と、失敗から生まれた
偶然の発見
お客さまからご要望の高かった、電源コードのない「ぴこぴこ」。コードレス化のために越えなければならなかった高いハードルとはどのようなことだったのでしょうか。
- 大西
-
都市ガスの主成分であるメタンを検知するには金属酸化物半導体(酸化スズ)センサーを400℃に加熱して、メタンを検知する反応を起こさなければなりません。これが電池駆動化の大きなハードルでした。電池で数年もの長期間動かすためには、現行型からさらに約1/1000の消費電力にする必要があったのです。
初期型センサーは2~3mm、現行型センサーは0.5mm。今でも、かなり小さいですよね。
- 大西
-
消費電力を少なくするには、センサーを小さくすることが効果的です。初期型は米粒くらいのサイズで消費電力は約1Wでした。AC電源式の現行型センサーの体積は初期型の約100分の1、消費電力は約0.2~0.04Wまで低減しています。このまま単純にセンサーを小さくするだけでは、消費電力をさらに3桁も低減するのは難しい。これまでの技術の延長線上では無理だということから、ガス警報器のコードレス化は永年「夢の技術」と言われてきました。
電子顕微鏡で見た、メタン高感度酸化スズ薄膜の断面
大阪ガスだけでなく、多くの家電メーカーがガスセンサーの薄膜化に挑戦されたとか。
- 大西
-
センサーを抜本的に薄く微小化する研究に、国内外の大手半導体メーカーをはじめ多くのメーカーが取り組みましたが、いずれも成功には至りませんでした。メタンに対して大きな感度を得ることが難しく、また、感度が変化しやすかったことから、「薄膜ガスセンサーの実用化は困難」と言うのが業界の常識となっていました。当社でも、大きなメタン感度を安定して得ることに苦労し、研究開発を一時中断したという歴史があるんです。
薄膜形成の実験中、とても重要な「偶然の発見」があったそうですね。
- 大西
-
実験を続けていたある日、メタンに関して高い感度を示すものが見つかりました。酸化スズ薄膜の断面を電子顕微鏡で見てみると、不思議な柱状の構造になっていることがわかりました。これは圧力換算ミスをしたことにより生まれた「偶然の発見」なんです。
圧力換算ミスの原因は何だったのですか。
- 大西
-
私たちは、真空中に少量のアルゴンガスを注入して酸化スズ薄膜を製造する研究をしていました。ある時、アルゴンの量を誤って過剰に注入したところ、無数の小さい柱が林立したナノサイズの柱状構造の酸化スズ薄膜が形成できました。ちょうどその頃は圧力の単位を世界的にSI単位系に統一することになった時期で、従来のTorr(mmHg)単位からPa(パスカル)単位に変換する計算を一桁間違えてしまって。普通は間違った条件で製造したものを計測することはしないと思いますが、セレンディピティーを大切にして、計測してみたことが大きな発見につながりました。これをきっかけに、薄膜作成条件を最適化した結果、感度が非常に高く、長期的安定性も高い酸化スズ薄膜を得ることに成功しました。
ずいぶん昔は、お酒のお燗(かん)でガス警報器が鳴るということもありましたね。
- 野中
-
当時のセンサーはアルコールや水素などにも反応していました。ある時期、兵庫県で誤報が多く発生し詳しく調べてみると、「いかなごのくぎ煮」が原因でした。センサーがみりんに反応したんですね。
誤報を抑える技術開発の過程においても「偶然の発見」があったとお聞きしています。
- 大西
-
当初は、メタンと水素の両方を検知するセンサーを開発しようとしていました。このセンサーはメタンと水素の感度を等しくする必要があるため、メタンと水素を同程度透過する触媒層の研究をしていたのですが、触媒を合成するときになぜか間違って百数十度も高い温度で焼いてしまったんです。その結果、メタン以外を酸化除去する性能が高くなり、メタンを酸化する能力だけが失われた触媒が得られました。このメタン以外を選択的に酸化除去する触媒を発見したことで、メタンのみを検知するセンサー開発に着手することになりました。そして、誤報の原因となる成分の感度を大きく抑制できるようになったんです。
- 野中
-
ここでも、セレンディピティーを大切にして、「偶然の発見」がもたらす画期的な可能性に気づいたことが研究開発の大きな一歩につながりました。
省電力化の実現と、待ち構えていた大きな壁
省電力化を実現するためにMEMS技術が必要だったそうですが一般的にMEMS技術とはどういうものでしょうか。
- 大西
-
MEMSとはMicro Electro Mechanical Systemsの略で微小電気機械システムのことです。一般によく使われるのは半導体センサーを小さくするというもので、ゲーム機のリモコンの動きを感じ取るセンサーやスマホのスピーカーなどにも使われています。
優れたMEMS技術を持つセンサーメーカーと、どのような経緯で共同開発されることになったのですか。
- 大西
-
実は、私たちの開発した技術の実用化開発を、当時警報器やセンサーを作って頂いていたメーカーさん数社に持ちかけたところ、「こんなものが使い物になるはずがない」、「当社では薄膜化センサーの量産化は難しい」などの理由でどこからも断られ、警報器用ガスセンサーとしての実用化開発はなかなか進みませんでした。ところが、当社が作製した「メタンを高選択性で検知できる薄膜化センサー」が当時の国立環境研究所さんの環境中微量メタン計測事業に採用されたことが新聞に掲載されたところ、MEMS技術を駆使して微小な領域だけを局所的に加熱できるマイクロヒーター技術を開発されていた富士電機さんが着目されまして。その後すぐに、富士電機さんから「両社のそれぞれの技術を組み合わせることで省電力センサーを開発しませんか」というお申し出を頂いたことが共同開発のきっかけとなりました。
今回の共同開発で生み出された省電力センサーのチップはかなり小さいですよね。
- 野中
-
センサーのチップは丸いシリコンの板の中に小さな部品の構成を作り込み、あとからバラバラにするという方法で作られます。CD一枚分の面積に数千個のチップが並んでいる感じですね。右の写真がその中の一個を拡大したものです。チップの中央の丸く盛り上がったところの中に酸化スズ薄膜があるのですが髪の毛1本分の面積と同じくらいなんです。
省電力センサーのチップの拡大写真。
チップの下にあるのは人の毛髪(太さ約0.1mm)
ここまで小さくしなければならなかった理由とは何でしょうか。
- 大西
-
省電力センサーは髪の毛1本分くらいのわずかな面積の中に柱状の酸化スズ薄膜があって、その上に触媒層が乗せてあります。この感応部を約百µmまで小さくすることにより局所的に400℃に加熱することで必要な電力を小さくしました。従来機は常時、電流を流して加熱している状態で、熱してから400℃に達するまで数秒かかっていたんです。それに比べ、今回開発した新センサーでは一瞬で400℃に加熱することができ、確実にガスを検知できます。しかも1分間に数回だけ瞬間的に電流を流してガス漏れをチェックし、それ以外の時は電流を流しません。このように、センサーの駆動パターンを変更することで加熱時間を極端に短くすることができました。その結果、従来センサーと比べて加熱電力が約1/600になったのです。
省電力化を実現されるためにご苦労されたと思いますが警報器という商品ゆえの大きな壁もありましたか。
- 大西
-
警報器は保安機器です。いつの間にかガス検知ができなくなることはあってはなりませんし、逆にガス漏れが発生していないのに警報を鳴らすということが頻繁におきるとお客さまに大変なご迷惑をお掛けすることになります。そのため、不具合の発生率を徹底的に低く抑える必要があるんです。
家電製品などと比べ、警報器の故障率はかなり低いのでしょうか。
- 大西
-
たとえば家電機器には故障率というものがあって1年間にどのくらいの確率で故障が発生するのかを%で表します。しかし、警報器は100万分の1というPPM単位で品質管理をしなければならず、しかも設置から3~5年間、性能を保証しなければなりません。1980年の発売以来、市場で起きた現象や現場設置後に回収した製品の分析結果などを基に改良を積み重ね、現在のガス漏れ警報器の故障率は通常の工業製品に比べ、極端に低い水準に達しています。
年々、製品の安全性に対する社会の要求が高くなっていますね。
- 大西
-
このセンサーの開発中に、消費生活用製品に係わる重大事故の発生が相次ぎ、製品安全に関する社会的関心が高まりました。これを機に、製品の安全性や信頼性に対する社会的な要求レベルが格段に上がったのです。実は、研究を始めて約5年後には長期間電池駆動できる省電力化が実現可能であることが確認され、早速実用化を進めようとしていましたが、「市場実績のまったくない新センサーの採用は、これまで築いてきた警報器の高い信頼性を損なう恐れがあるのではないか」との声が社内で強くなったため、商品化に向けての計画が一旦行き詰まりそうになりました。 こうした状況を打開するために、市場に出す前に、長期信頼性を充分に確立する必要があり、市場での長期信頼性をラボにおいて短期間で評価できる手法の開発も必要になりました。製品に対し安全性をシビアに求めるという社会的ニーズは私たち開発者にとって、とても大きな壁でしたがチーム一丸となって研究開発を続けることで無事、乗り越えることができました。
高度な信頼性を確立するための技術開発
室温から一瞬で400℃まで加熱しても、センサーは劣化したり故障したりしないのでしょうか。
- 大西
-
一般的には、瞬間的に室温から400℃に上げるとすごく負荷がかかります。開発当初のセンサーでは、異なる素材を基板の上に積み重ねているため、急激な加熱・冷却を繰り返すヒートショックと他のストレスの組合せによりダメージを受けてしまう可能性があることがわかりました。5年間動かそうと思えば、数百万回のヒートショックが起きるので、積層構造と製造方法を工夫してそれに耐えられる素子を開発する必要があり、課題解決のために時間を費やしました。
長期の信頼性を評価するために、日本全国のご家庭に開発中のセンサーを設置し、データを収集されたそうですね。
- 野中
-
先程、お話ししましたが、ちょうどこの頃、製品安全に関する社会的関心が高まっていたことから、「NEDO」=国立研究開発法人 新エネルギー・産業技術総合開発機構が中心となり、高い信頼性を有しつつ電池で長期間駆動するセンサーを開発するプロジェクト「次世代高信頼性ガスセンサー技術開発」が立ち上がりました。このプロジェクトでは、全国約660世帯にセンサーを設置し、定期的に回収して特性変化を調べる取り組みが行われました。私たちもできる限り多くの現場でセンサー評価をしたいと考えていたので、そのタイミングをとらえてプロジェクトに参画させて頂くことにしたのです。
全国660世帯のご家庭に設置させて頂き、
多様な実環境で特性変動を調査
北海道から沖縄まで660世帯とはすごい数ですね。実際のご家庭における現場設置試験でどのような発見がありましたか。
- 大西
-
設置先の製品を半年に一度回収し、センサーの性能がどのように変化していくのかというデータを収集しました。通常の製品にはない、温湿度センサーや環境物質を捉える吸着剤も搭載して詳しく調査しました。すると私たちが想定していた環境と実際の台所環境とでは異なる点があることが判明しました。温湿度で言いますと、意外なことに北海道などの寒冷地ほど冬場はほとんど温度が下がらない。常に暖房しているからなんですね。また、沖縄はそれほど温度は高くなく湿度がとても高かったんです。
家族構成、在宅時間が長い短いなど、いろいろなご家庭がありますよね。現場設置とラボとの評価はずいぶん違いましたか。
- 野中
-
ラボで数年間センサー性能が安定していることを確認した上で現場設置したのですが、よく観察してみると2年ほどで一部のセンサーで性能が変化する兆しが観察されました。いちばん驚いたのは、複数のご家庭で、通常の台所環境では存在しないはずの環境成分が多量に存在していたことです。いろいろ調べていくと、部屋で特殊な溶剤を使った作業をされておられたり、廃棄物を大量に保管されておられるお宅だったんです。また、1日中、湯気がセンサーにあたっているようなご家庭もありました。
センサーの表面を汚してしまう成分として、どういうものを想定しないといけないのかをラボでいろいろ考えましたが、現場では私たちの想像を超えた驚きと発見がたくさんありました。
現場から回収したセンサーでどのようなことを分析されたのでしょうか。
- 野中
-
まず、現場から回収したセンサーで起きている変化を確かめました。それがどのような化学物質で起きるのか、またその変化を引き起こす原因は何かということについてかなり詳しく分析しました。そして、このような性能変化を生じさせないよう、センサーの改良を行いました。
改良されたセンサーはどのような方法で試験されたのですか。
- 野中
-
NEDOのプロジェクトでの設置期間は3年。改良したセンサーを使ってもう一度、現場設置試験をやり直すことはできません。そこで私たちは、実際の現場のストレスを短期間で再現するような試験方法の開発に取り組みました。
その試験とは加速評価と呼ばれる手法のものです。変化を引き起こす原因となるストレスを特定し、それをセンサーに与えることで同じような変化を短期間で起こせないかということに取り組みました。様々な条件で試験を行ったのですが20種類もの試験をしてそのうち正解はたった1つということも。しかも、適切な試験条件がわかったとしてもラボで試験したものが現場に置いたものと同じ性能変化現象を起こしていることを確認し、さらにそれが現場での何年に相当するのかということも確かめなくてはなりません。あるストレスの強度を変化させて、現場の3年で起きるものを1カ月程度で再現するのに必要な条件を調整するという試験を何度も行いました。
- 大西
-
その努力が実を結び、自分たちで開発した新しい手法を用いて、改良したセンサーの長期信頼性を検証することができたのです。
この開発で苦労されたことはどのようなことでしょうか。
- 野中
-
薄膜を用いたセンサー技術は世界初。世の中にお手本になるようなものがなかったんですね。センサーの性能が何の影響を受けてどう変化していくのか、まったく前例がなかったため、自分たちで想像し、探し当てていくことが大変でした。
- 大西
-
それまでの常識では実現は無理と思われていたことに挑戦することをおもしろいと思う性格なので、技術的な面で特に苦労があったとは思っていないんです。しいて言えば、お客さまから強いニーズがあった製品でありながら、様々な障害を乗り越えて実用化するまでに長い時間がかかったことでしょうか。実は、開発が継続できなくなりそうな危機的状況を迎えたことが何度もありましたが、この技術を実用化するのが自分の大きな使命であるとの信念を持って、幸いなことに、それらの困難な状況を打開することができました。無事、発売の日を迎えることができたのは、そのようなピンチを迎える度に、支援して頂けた方々のお陰です。
ご自身の夢や目標についてお聞かせください。
- 野中
-
日本はもちろんですが、世界中の警報器を電池式のものに置き換えていきたいですね。また、今回のセンサー技術をガス警報器以外の用途で活用できるよう、さらなる挑戦を続けていきます。
- 大西
-
これまで不可能と言われ続けていたガスセンサーの薄膜化を成功させた今回の貴重な体験を活かして、エネルギーの世界に大きなゲームチェンジを起こす新たな技術開発にチャレンジしていきたいと思っています。
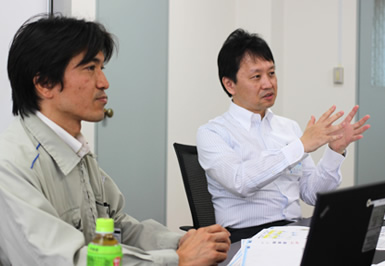
TAG SEARCH
キーワードで探す
- 家庭用ガス機器を
さらに進化させる -
家庭用ガス機器を
さらに進化させる 給湯・暖房・乾燥 調理 スマート機器 燃料電池
- 業務用・産業用ガス機器を
さらに進化させる -
業務用・産業用ガス機器を
さらに進化させる コージェネレーション 空調・厨房 バイオ・水処理 工業炉・バーナ エネルギーマネジメント・IoT
- ガス製造の安全・経済性を
向上させる -
ガス製造の安全・経済性を
向上させる 冷熱利用 プラントマテリアル 発電技術
追求する
- 先進的な取り組みで
次世代を創っていく -
先進的な取り組みで
次世代を創っていく 材料開発 計測 シミュレーション・データ分析 フードサイエンス 材料評価
- 環境・脱炭素社会の
実現に貢献する -
環境・脱炭素社会の
実現に貢献する メタネーション 水素・アンモニア バイオガス エネルギーマネジメント 再生可能エネルギー
知的財産状況
- グループ会社の技術
- 株式会社 KRI 大阪ガスケミカルグループ オージス総研グループ