~コンパクトで高効率な家庭用燃料電池の開発~
家庭用燃料電池
「エネファーム type S」
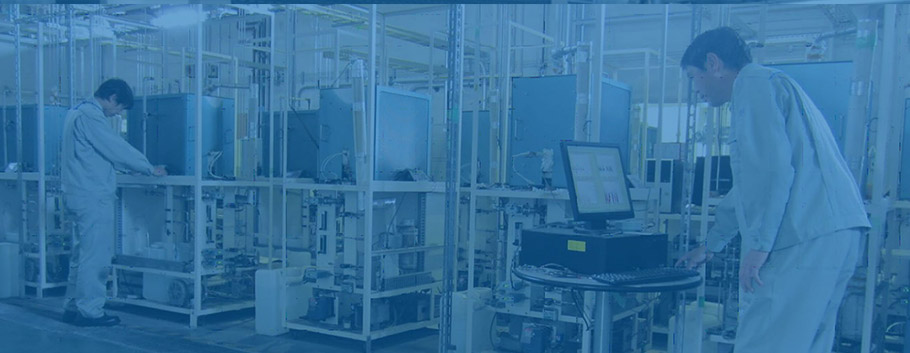
DEVELOPER INTERVIEW
開発者インタビュー
コンパクトで高効率な家庭用燃料電池の開発
家庭用燃料電池「エネファーム type S」
2012年4月に発売した「エネファーム type S」は、2003年発売の「エコウィル」、2009年発売の「エネファーム」に次ぐ大阪ガスで3種類目の家庭用コージェネレーションシステム。
「エネファーム type S」は先行の2種よりも発電効率の高い固体酸化物形燃料電池(SOFC)であり、初号機は2012年4月に発売しました。それ以降も、高効率化、コストダウンを進め、2013年、2014年に新機種を発売してきました。
これらの開発、改良に携わった技術者たちが、さまざまな課題をどのように解決したのか、「エネファーム type S」の基幹部となるセルスタック・ホットモジュール部を担当した鈴木氏、井上氏、システムを担当した安原氏、岩見氏に、商品化への開発秘話を語って頂きました。
MEMBER
リビング事業部
-
商品技術開発部
SOFC開発チーム
シニアリサーチャー 工学博士
鈴木 稔 -
商品技術開発部
SOFC開発チーム
副課長 リーダー
井上 修一 -
商品技術開発部
SOFC開発チーム
副課長 リーダー
安原 健一郎 -
商品技術開発部
SOFC開発チーム
係長
岩見 潤
SOFCを使った家庭用コージェネレーション
システムの開発へ
従来のPEFCを使った「エネファーム」より、高い発電効率を目指して、SOFCを取り入れた「エネファーム type S」の開発を当初から主導してきた鈴木さんですが、どのような経緯で取り組みはじめたのでしょうか。
- 鈴木
-
SOFCはセラミックスを電解質とする燃料電池です。電気を発生させるセルスタックの動作温度は、現在は750度くらいが主流ですが、以前は900度程度。1990年代の半ば頃から、温度を下げる技術が世界各地で出てきました。より扱いやすくなり耐久性も増したんです。セラミックスそのものは、小さいほうが信頼性が高いこともあって、SOFCも小型化する流れが、90年代後半から出てきました。
- 井上
-
その上、SOFCではセルスタックから出る熱を使って、燃料である都市ガスの改質ができ、より高効率も期待できる。小さくて良質なセルスタックをつくっていた京セラさんと、家庭用SOFCの共同開発が始まったんですね。
- 鈴木
-
当時、PEFCが先行していましたが、SOFCだったらこういうことができるはずという未来像が、京セラさんと我々との間に共通認識としてありました。そこで最初の2年間では試験機をつくって、実際の住宅に入れて高い性能を実証しようと。
- 岩見
-
その結果として、発電効率49%を実証試験で達成したんですね。2006年に発表した時は、とても衝撃的だったと聞きました。
- 安原
-
私は当時PEFCの開発チームにいたのですが、数字を聞いて驚きました。これは本当に継続的に動くのだろうかと半信半疑(笑)。それぐらい驚異的な数値だったんです。まさかその後に、自分がそのチームに入るとは思ってもいませんでしたが(笑)。
- 鈴木
-
当時は、耐久性の検証はできていなかったのですが、それでも最初の試験で計画した3000時間はちゃんと動かせていましたね
- 井上
-
当時、業界の常識では、100kWとかの大きなSOFC。それをいきなり1kWで実用化に踏み出したというのは衝撃的だったと思います。しかも家庭用では、大型とは違ういろいろな負荷がかかります。たとえば、頻繁に起動・停止が繰り返されるとか。家庭の電力需要に追従したかたちで24時間きっちり動くというのが、当時では信じられない世界だったでしょうね。SOFCの新しい流れをつくった出来事だったと思います。
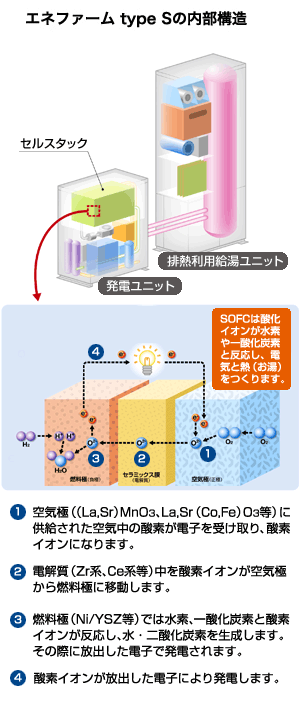
商品化に向けて「46.5%の発電効率」と
「10年間の耐久性」を実現
SOFCの商品化に向けては、家庭用ということで、700W機で「発電効率45%」と「10年間の耐久性」が目標ということでしたが、結果として発電効率46.5%、総合効率は90%で、耐久性の目標も実現しましたね。
- 井上
-
セルスタックの耐久性に関しては、試作したものを丸1年、2年と動かして、劣化の状況をモニタリングし続けました。最初の仕様、次の仕様、その次の改良仕様のもの、全部並べて、延々と動かし続けるんです。今もまだやっていますが(笑)。
- 鈴木
-
どんどん試験台数が増えいった(笑)。耐久試験と改良を繰り返すことで、性能が上がり、劣化のスピードも緩やかになってきましたね。
- 井上
-
劣化に関する一番の課題は、セルとセルをつなぐ金属部分(集電材)が酸化し、それが原因で電圧が落ちること。最終的には金属表面に特殊なコーティングを施すことで解決したのですが、こうした大事なところは、メーカーさんとともに、僕らも開発者スタンスでやっていきましたね。
- 鈴木
-
燃料電池では、加速試験で時間を短縮して劣化の程度を測ることが難しいので、やはり以前の仕様でも1万時間、2万時間と地道にデータを取っていくことが必要。今では、4万時間を越える、かなり昔の代のものあるんですよ。
- 井上
-
このデータの積み上げは、自信にもなるんです。この検証がなければ、どのタイミングで劣化が起きるのか、劣化が始まった場合、機能低下の曲線はなだらかなのか、急激なのかわかりません。実際にデータを積み重ねていかないとわからないことなんです。
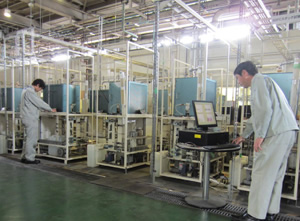
大阪・酉島の研究所内でのセルスタックの耐久試験の様子
- 安原
-
耐久性については、お客さまの実際の使用時に、あまりにも頻繁に起動・停止をさせると機器に負荷がかかり、影響が出る可能性もあるので、発停回数をできるだけ減らすシステムを作り上げることも必要でしたね。
- 鈴木
-
さらに、起動後、発電前にスタックを高温にするときにエネルギーを使うので、起動停止を少なく発電時間を長くするほうが省エネメリットが大きいんです。
- 安原
-
そうしたメリットをお客さまにどう伝えていくか。起動・停止を頻繁に繰り返されるお客さまに対しては、例えばリモコンの表示画面にメッセージを出すなど、より効率よく使っていただけるよう、運用面からの工夫にも努めました。
- 鈴木
-
私と井上はセルスタックとその周辺の改良に目が向いていますが、実際に使用される環境、運用面、そういった視点で、意見をどんどん出してくれる人が身近にいるのはとても重要です。
- 安原
-
営業や施工など、現場の声を吸い上げてくるのも私の役割ですから。
- 井上
-
安原さんの評価をクリアしたら、完成度が上がってきた実感がありますね。(笑)。
最適システムを構築してコンパクト化と
施工性の向上を実現
機器の仕様はどのように決定したのですか。
- 安原
-
最初は1kWの出力で想定していたのですが、一般的なお客さまの電気使用量を考えるともう少し落とせるのではということから、2006年に現在の700Wになったんです。
それが機器全体のコンパクト化や機器コストの適正化にもつながった。貯湯タンクの大きさをより小さくできました。それとは別に、家の敷地内により設置しやすいよう、機器本体の奥行き寸法をできるだけ薄くしたいというのもありましたね。
- 井上
-
セルスタックも、それまで4列だったセルを2006年頃に2列にしたのは同じ考えから。1列のセルの数を増やし、厚みも削減しました。
- 安原
-
セルスタックを納めたモジュールを包む断熱材も、当時PEFCで試用されていた高性能のものに変更し、スリム化を図りました。当初は施工性やコストが高くなることも懸念されたのですが、使用量を見直したことで、結果的にコストダウンできました。
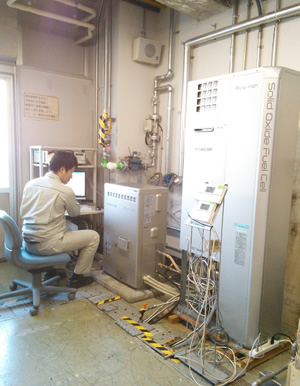
大阪・舞洲の研究所内でSOFCシステム評価試験の様子
- 岩見
-
そうした努力の末の発売後、初号機は省エネ大賞の経済産業大臣賞をはじめ、いろいろなところで賞をいただきましたね。販売台数も、うれしいことに比較的早い段階で目標近くにまで伸びました。
- 安原
-
実験室を飛び出して、商品になったんだなあという感慨はありましたね。SOFCの家庭用で10年もつものが商品として出たことは、専門家の間でもかなりインパクトがあったと思います。
- 井上
-
僕らはセルスタックの担当なので、まだまだ途上という気分、感慨に浸る間がない(笑)。実際に商品化されると、今まで数台レベルだったのが1000台のレベルで世に出ていくわけで、そうなって初めてわかる課題もある。それに加え、次世代機の検討もあり、しばらくは頭がいっぱいでした(笑)。
お客さまのニーズに合わせた改良機開発と
さらなる挑戦
- 岩見
-
このチームでは私はまだまだ新人で、加わったのは2011年。初号機には、発売前の短い期間だけ関わりました。
- 鈴木
-
その前は開発とはまったく違う部門にいたからね。
- 岩見
-
ここの燃料電池技術は世界トップランクでSOFCの商品化も近いと以前から注目していて、自分もぜひ関わりたいと考え、自ら異動を志願しました。
- 鈴木
-
いまではメーカーさんとの間で、仕様内容などをまとめる主担当。改良機の開発には大きく関わっているよね。
- 岩見
-
改良機では、システムの再検討などを主体として、よりお客さまのニーズに合った機能をプラスしていくことも課題でした。停電時の自立機能やLPガスへの対応もそうですし、外付けだった電装基板をうまく内蔵化すれば、コストを下げられ施工性も良くなるのではとか、いろいろと試みましたね。
- 安原
-
基板の内蔵については、レイアウト次第で内部スペースが使えるのではないかと、メーカーさんに提案しました。ただ、外側はすっきりするけれど、今度は配線が一カ所に集まり設置時に施工しにくくなる問題が出てくる。そこは、岩見君が中心になって、メーカーさんと施工サイドの要望をすりあわせながら、いまのかたちを実現した。
- 岩見
-
デザイン的にもさらに良くなったということで、グッドデザイン賞も継続していただくことができましたね。
- 安原
-
今後の一番の課題は、やはり、より一層の低価格化を実現して、お客さまの裾野を広げていくことですね。さらに小型化を進め、将来は集合住宅にも設置していけるようにしたいという夢もありますが、そこで求められるコストのレベルはもっと低くなるし、求められる機能のレベルや信頼性はさらに高いものになるでしょうね。
- 井上
-
コストに関しては、今はセルスタックの影響が大きいので、発電性能をさらに上げながらコストを下げるとことを共にやっていく。その先にしか解はないでしょうね。
- 岩見
-
最近まで、高温部分には樹脂部品を使ってはいけないという規制がありました。しかし規制緩和の働きかけにより、樹脂部品の使用が認められたことで、コストが大きく下がる見通しが立ちました。今後もそういった面での規制緩和を、技術者の側から安全性を示し、働きかけていくことも試みたいですね。
- 鈴木
-
発電効率がさらに上がると、電気とお湯との関係上、もう少しタンクを小さくしてもメリットが出せる。するとよりコンパクトにもできる。コストダウン、高効率、コンパクトを全部追っていっても、必ずしも相反するものではない。ということで、我々に今後も求められているのは、次のステップへの絶えざる挑戦ということです。
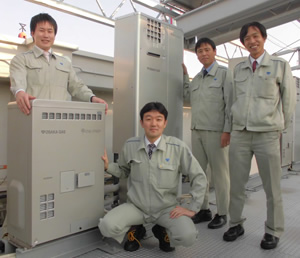
TAG SEARCH
キーワードで探す
- 家庭用ガス機器を
さらに進化させる -
家庭用ガス機器を
さらに進化させる 給湯・暖房・乾燥 調理 スマート機器 燃料電池
- 業務用・産業用ガス機器を
さらに進化させる -
業務用・産業用ガス機器を
さらに進化させる コージェネレーション 空調・厨房 バイオ・水処理 工業炉・バーナ エネルギーマネジメント・IoT
- ガス製造の安全・経済性を
向上させる -
ガス製造の安全・経済性を
向上させる 冷熱利用 プラントマテリアル 発電技術
追求する
- 先進的な取り組みで
次世代を創っていく -
先進的な取り組みで
次世代を創っていく 材料開発 計測 シミュレーション・データ分析 フードサイエンス 材料評価
- 環境・脱炭素社会の
実現に貢献する -
環境・脱炭素社会の
実現に貢献する メタネーション 水素・アンモニア バイオガス エネルギーマネジメント 再生可能エネルギー
知的財産状況
- グループ会社の技術
- 株式会社 KRI 大阪ガスケミカルグループ オージス総研グループ